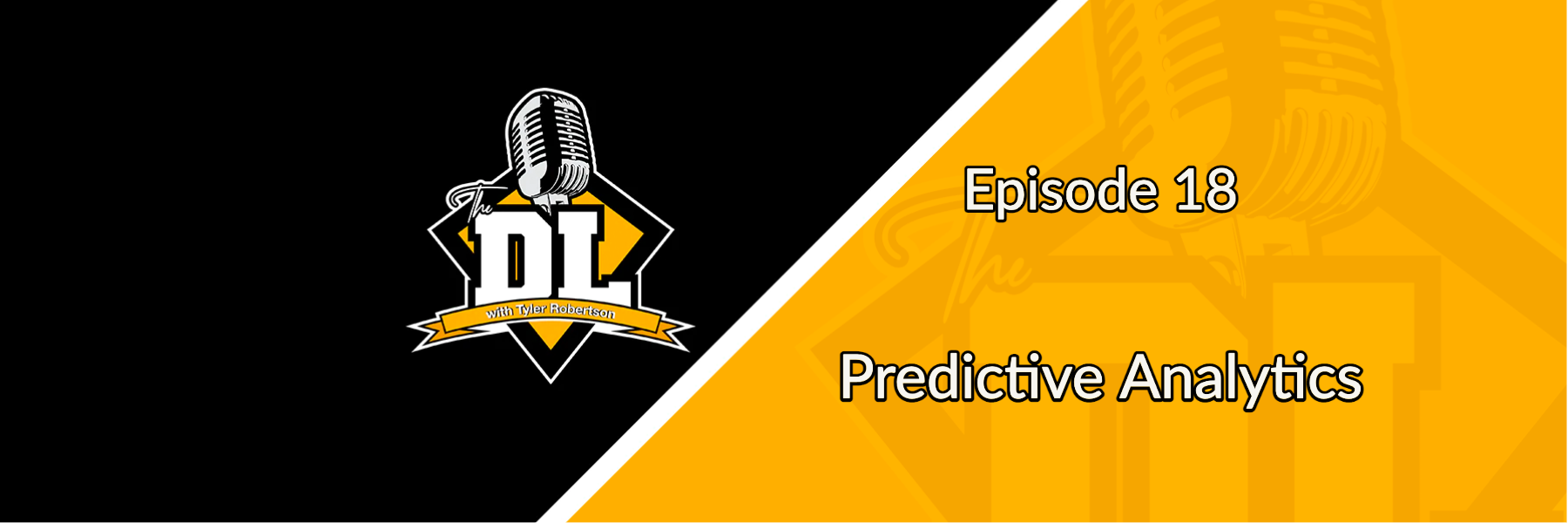
Predictive Analytics - The DL S3E18
Predictive Analytics - The DL S3E18 is now available on Apple Podcasts, SoundCloud, IGTV, and YouTube.
In this episode of The DL, Diesel Laptops’ Founder and CEO, Tyler Robertson, is joined by Jon White, President at Jon White Inc.
Please like, subscribe, and share. If you have questions or would like to learn more about a particular topic, drop a comment and let us know.
As always, thank you for watching and listening!
CONNECT WITH JON WHITE:
LinkedIn – https://www.linkedin.com/in/jon-white-9b659a1b/
Website – http://www.jonwhiteinc.com
Transcript for Predictive Analytics - The DL S3E18:
Tyler Robertson:
All right. Here we go. Welcome to the DL. I am your host, Tyler Robertson coming to you from our studio here in South Carolina. This is the podcast show where we talk about everything going on in the truck repair world. And one of the big things that a lot of people are asking about is predictive analytics. When's it going to happen? What's it like? How's that going? And in general, I think it's good that we bring someone on here that's been involved in the space of diagnostics and fault codes and data buses for over 30 years. So I brought an expert on the show today. I would like to introduce everybody to Jon White, who has his own firm called Jon White Incorporated. So Jon, welcome to the DL. It's great to have you on here, man.
Jon White:
Thank you. Thank you. Thanks for having me, Tyler. It's a pleasure to be here and share some history and some of my knowledge.
Tyler Robertson:
Well, let's just go back in time a little bit. I think you started in the '80s working on these things. Can you talk a little bit about
Jon White:
Yeah.
Tyler Robertson:
... how we got here.
Jon White:
Well, actually, I started working with Predictive Analytics on nuclear submarines. After graduate school, I was working for the Naval Ship Engineering Center, and I was tasked to work on electrical systems for the Atlantic and Mediterranean submarine fleets. And I did some predictive analytics, applying financial modeling techniques to reliability data on generator systems on some classes of submarines. And it worked pretty good, and published a paper. Some people in the trucking industry got hold of it. And I moved to the trucking industry about 1976/77 with some service bureaus, and then shortly thereafter with Ryder. And ever since that point in time, I've been working in data technology around minimizing cost, minimizing unplanned downtime, and trying to forecast component failures.
Tyler Robertson:
So when you first got involved in the heavy truck space, what was the problem that you first saw when you first got into the heavy truck space?
Jon White:
Well, I had a small company called Microflex in the '80s, and we were doing work for the Big Three in diagnostic technology. And with GM and Chrysler and Ford, you've got the ability to easily diagnose problems when there's a vertical vehicle, a vertical asset. But as the electronics started to move into the heavy truck in the early to mid-'80s, what you had is you had a vehicle, an asset, with multiple components using electronic controls, and there was two or three problems. One was communication in the vehicle. The second was to be able to diagnose problems with a device off board. And then the third was programmability.
And so, because I'd been a previous Ryder employee, I went Ryder and talked to him about this problem. And we put together a consortium between Ryder, Caterpillar, Cummins, and Freight Liner, and we worked on a defacto standard for the industry. And we did this in a laboratory environment. And the goal was to establish a common communications platform in the vehicle, and a way to interpret and provide diagnostic technology for the mechanics. And we served this to SAE in a press release in 1987, and it was embraced by the industry.
So it went to committee to SAE. And over the course of the next two years, the original data link standards J 1587, 1708, started to evolve. And over the years it became J 1922, and now it's known as J 1939. So the committees that worked on that were very... Almost all the major OEMs were involved in that process. And it stuck and it worked good. There was still some issues around a universal diagnostic platform, which you have to this day, and others, and so it worked really good. And the feeling is that J 1939 will be around in the near term.
Tyler Robertson:
So, when I go back in time here a little bit, we still get phone calls from customers who have trucks in the early '90s, specifically Detroit Diesel and a DDEC1, and they're like, Hey, I got this weird looking connector. What tool do you sell that works? And we just always say, nothing because even Detroit doesn't make software that connects to a DD 1, those original ones.
Jon White:
Right.
Tyler Robertson:
Was this a time period when people were all having their own physical connectors and were they all having their different software? Was it like a mixed bag at first and it really didn't seem to really standardize to the early '90s? Is that how that played out?
Jon White:
That exactly right. And then as you move fast forward to today, Tyler, you've still got... As you look at the J1939 data link, you've still got a lot of proprietary information floating around on that device, proprietary OEM Cams that are loading that data. And so anybody that's working with diagnostic or, let's say, interpreting fault codes on the vehicle's got that problem of proprietary codes. And it's an issue. I worked with a fleet in the North East recently and about 40% of the codes that were coming across the data link were proprietary. And we worked with you to try to get some of them defined.
Tyler Robertson:
Yeah. It's
Jon White:
And the other thing that's emerging that is an issue for fleets from my perspective of being out there working with fleets, is that a fleet will get, let's just use the term fault code, diagnostic trouble codes. These are rays of... Fault codes will come from so many different sources. If he's a Detroit, I suppose he is running Detroit Engines. So he is got the Detroit Connect. If he's got a telematics device, that's providing diagnostic trouble codes. If he's got a fleet maintenance system that's integrated with the telematics device, he's getting the codes that way. So the fleet managers today are overwhelmed with all these different sources of data and all the different sources of dashboards, and ways to interpret the data. And so it's a little bit of a hodgepodge out there right now.
Tyler Robertson:
Yeah. I want to break it down a little bit for the audience here as well. And a lot of times people ask us, heavy trucks is just like cars, are just bigger. And I'm here to tell people computer-wise, they're not. So, first of all, we're not vertically integrated. So when you buy a International, it's not an International ABS system, it's not an International engine, maybe it is, it's not an International transmission, it's not an [crosstalk 00:08:50] International advanced driver-assist system. And that's really the complexity. And not only that, I guess when we talk networks on a vehicle, I don't know an easy way to explain to people, except for the fact that there are different protocols, like me and Jon are sitting here talking about J 1939, J 1922, J 1708 and all these things.
That's a bigger thing, but it gets complicated because certain manufacturers like the ABS guys, they use J 1708, and the truck guys, the engine guys, they're using J 1939, and now UDS comes along, and we're using UDS. And all of a sudden you've got different networks, all doing different things, yet this truck needs to operate seamlessly down the road. And I know one of the parts we struggle with is, even when we work with telematic providers, they don't know how to look for all those things. They don't know where all the codes are. They don't know where all the data streams are. And again, like you said... You mentioned the word proprietary. Can you explain to everyone what you mean when you say proprietary fault codes to clarify that a bit?
Jon White:
Well, I can't give a specific example right off of the top of my head, Tyler, but I know that when you look at the data link, you'll see a fault code and the telematics provider that's producing information or reporting fault codes that are showing up, it'll just show up as undefined. And so you have to go to another source.
Tyler Robertson:
Yeah.
Jon White:
And so, just like you say, if you've got an electronically controlled transmission, you've got the engine that's working with all its electronics, you've got an ABS system, now we're all the smart trailer data, and so you've got a hodgepodge showing up on J 1939. And some of the initial goals of J 1939 are slipping away because there's no standards out there that cover everything. I don't know what the current county is, but my guess is there's probably 20,000 codes, more.
Tyler Robertson:
Yeah. I
Jon White:
Scores of thousands.
Tyler Robertson:
Yeah. I can actually answer that question because that's our mission here at Diesel Laptops, is to catalog every fault code that exists and have repair information. So, I can tell the audience listening to this, there are over 100,000 unique fault codes that exist on commercial trucks.
Jon White:
There you go.
Tyler Robertson:
And if you look at off highway, that number is magnitudes larger, maybe even 10 X larger than the on highway truck market. And what I've tended to learn here is that those known codes, those are the SA defined ones that all the OEMs are supposed to use and supposed to do. But then there's the things that aren't defined by the SAE. So the OEMs just decide what codes to use and what those codes mean. So you can have a six-digit SPN code with Freightliner and it can mean something totally different with International if they both happen to pick the same six-digit code. So there's a lot of complexity that I think the average person doesn't understand. They just look
Jon White:
Right.
Tyler Robertson:
... at a tool and be like, it's not working. It's not reading all my codes, or, it's not doing this or not doing that. They just don't know. It is a very complex thing. And I'm telling listeners here, there are companies like mine, many of us, that have a lot of engineers trying to decipher all this stuff, and we get no information from the OEMs. So every time a new truck model comes out or a new year comes out, it's like starting all over again and all of us are out trying to figure it out.
Jon White:
Yeah.
Tyler Robertson:
So, Jon, answer this question. I know why I need codes and our customers, they're trying to fix things that are broken. Why are other companies wanting to get data or fault codes off of the vehicles?
Jon White:
Well, ultimately, you want to have a scenario whereby a fault code, or a persistent fault code, or an array of fault codes create an actionable insight to prevent a breakdown on the road, and even going a step further to prevent an unplanned downtime event, whether it's on the road or not. And so the ability to just simply look at fault codes, and I'm not talking about real time data right now, but just looking at fault codes, there is some benefit in correlating fault codes, looking at persistence, severity, population, density of these fault code to determine if a real event is going to occur, if there's going to be a problem.
So the term filtering fault codes, or filtering diagnostic codes has become like a thing in the industry because there's so much data on the data link that's showing up. If you were to look at all of the codes, some of them are meaningful, some of them are not. So there is some value in looking at just fault codes, filtering them and looking at the density, and trying to determine and assess whether or not here is a problem occurring in the vehicle.
Tyler Robertson:
So Jon, when I talk predictive analytics or predictive maintenance, when I talk to customers that are especially fleets, they're like, oh yeah, we do that. We look at repair orders and we know this alternator fails at 250,000 miles. So we just replace it early. And I'm always like, okay, that's cool. And that's what I thought the world was. And then you actually explained to me, and you were like, "Tyler, before a fault code occurs, there's things that are going on. The reason a fault code occurs is because a threshold got hit." And the way you really explained that to me was, "Well, if you watch the values go up before you get to that code, you can actually get ahead of it." So where is that technology? Is that doable stuff today? Is it future? Where is it at?
Jon White:
The data streams that are produced in the vehicle over time, present an opportunity to alert a fleet manager or to alert an operator to a problem that is emerging before a fault code occurs, and correlation of these data streams cross-analyzing these data streams can very often help predict an imminent problem before a fault code emerges. A simple example of this is, if you were looking at the data streams in real time or near real time of say, engine temperature, engine speed, and cooling temperature, those three data elements should track relatively the same. So if you're tracking engine speed, the oil temperature and the cooling temperature, and all of a sudden the cooling temperature diverges from this path, you would know that, well, there's something going on in the cooling system.
So this can in and of itself generate an alert that is actionable, possibly before a fault code emerges. And that's where true predictive analytics, I think, comes about, in being able to predict a problem before the fault code emerges. And that puts a whole nother level of complexity and that's where predictive analytics in the future is going to provide value, I think, real value to the fleet operator.
Tyler Robertson:
So Jon, I've talked to Pit Stop and other companies out there that are doing these things. Are they able to look at similar trucks and use that as a base to try to judge what my truck should do? Like, if there's 500 trucks and we're all the same, and mine's doing something weird, do they compare it to the other truck populations, or are they just going to look at your truck in particular in these cases?
Jon White:
I think it's both. I think you can do a singular data point with one truck. In any statistical analysis, if you've got a large population, the data's going to be more reliable. But the bottom line that so many people miss, from my standpoint, and looking at what's going on in the industry right now, Tyler, is that you can't do thorough and a precise predictive analytics without the knowledge base from the component engineer, the engineer that really knows the system. And so many times, if you're trying to develop, let's say, an algorithm that learns about the behavior of the components in the vehicle, so many people do this in a void, without the expertise of an engineer. Even if you're cross-correlating fault codes, or you're trying to do an AI learning model, you have to have the knowledge base at the outset. It's just not about presenting data, what is meaningful, what's not.
Tyler Robertson:
So, let's talk about the data coming off the vehicles. So we've looked at telematics data and we've looked at things, and it always seems like we get 70% of what we need, right? Like, we want to see this other thing over here, but it's a proprietary pit or proprietary value. The geo tab or whatever device it is, doesn't quite know where to look, so it's not getting us that data. Do you guys run across that as well of either inconsistent data or not all the data you need to make these things work, or what you guys are seeing, is it enough to get started in this field?
Jon White:
Well, you mentioned about an ingredient that is... It has to be predominant in these learning models. And that is the feedback from the historical work orders. So if you have an insight and you say that it's going to be a cooling system issue, let's just say, and you do the repair, or you don't do the repair, the feedback from that decision-making has to come into the learning model, so that you've got three key elements that are part of this predictive analytics. You've got the data stream itself, you've got the diagnostics, and then you have the work orders that are result of all that. And the work orders provide the feedback about what the AI or learning models can derive from your historical decisions that you've made. And the more you can look across the industry with similar trucks, the higher the precision and reliability of these insights are.
Tyler Robertson:
And that makes total sense. So, to me, this is a three-piece puzzle. It's getting good, clean quality data off the vehicles. It's having a great AI machine-learning and predictive analytics tool. But at the end of the day, like you mentioned earlier, someone needs to look at it and actually do something with that data. And I think that's been another missing piece, because oftentimes these software companies are doing the AI machine learning, they don't exactly earn experts on how to fix trucks. So in my opinion
Jon White:
Exactly.
Tyler Robertson:
... there needs to be a bridge gap there. How's that working out in the field and what you see out there?
Jon White:
Well, I've felt like, and I've shared this with you before... I think that it's like a three-legged stool, unless you've got all three legs there, it's going to, it's going to wobble. And so many of the service providers have a twofold problem. One, not only getting accurate data from the vehicle and being able to define it, but also getting accurate data from a work order system. And think about how many variations of work order systems are predominant in the industry. You've got, you've got TMT, you have, on and on and on, that are out there. And so the challenge gets to be when you move into this area, it's all about interfaces. It's all about interfaces to be able to effectively do this. And I think that's going to be there for a while, the need to have interfaces that provide that feedback loop.
Tyler Robertson:
Yeah. I want to
Jon White:
Because ultimately, just let me throw in one more thing, I think ultimately, over the next 10 years, Tyler, the industry's going to move more to prescriptive maintenance, rather than just simple preventive maintenance. 10 years from now, when a vehicle comes into the shop, you're going to have some prescriptions for what to do, rather than just change the oil, or engine, in or whatever because of the amount of intelligence that the vehicle... It's like a moving local area network.
Tyler Robertson:
Yeah. And I think you bring up a great point. In a order to do all this, you've got to get data off the vehicle, and with 3g, we could do a little bit, 4g and LTE, we could do a lot more. And now 5g is coming here, which gives us even a bigger pipe and more ability to get things up to us, and costs have come down and data networks and what it costs actually, have a device in a cab all the time. So this is a really super interesting puzzle because you need a lot of experts and a lot of things with that closed loop, like you talked about, in order for this thing to really, really work together. So if there's a maintenance manager, a fleet manager, a fleet owner that's listening to this, and they want to start exploring this and talking to people about what's possible, what's not, is there some companies you'd recommend, or what should be the first thing they do if they're like, man, I really want to learn more about predictive analytics?
Jon White:
Well, I think that right now, what I'm seeing in the industry is, there's two companies that are predominant in predictive analytics. It's Pit Stop and Uptake and they've invested time and money in their data science groups. And this is not a modest endeavor to build an AI learning engine because of the different issues that we've talked about, both in the vehicle and off the vehicle. So I think that as we move forward, there'll be some OEMs that have their own predictive analytics capability. But I think that it's going to be few and far between that are going to be effective, because lots of times is, you talk to somebody that's in the telematics business and they say, yeah, we do predictive analytics. Well, what do you do? Well, we read the fault codes and tell you how many times they're occurring. It almost gets to be, so what, if you do that? So, we're at the point where, as an industry, we can, I think, do more than that.
Tyler Robertson:
Yeah. I, 100% agree with you. We're like in day one or day zero of learning predictive analytics and getting all this data and putting things in there. I got a lot of confidence, five years from now, this whole thing is going to look entirely different than it does today. The technology moves fast. As you said, a lot of smart people, a lot of money being thrown at this problem, because everyone knows where this whole thing goes to. Jon, if people want to find you, they want to reach out to you, what's the best way to do that?
Jon White:
I didn't understand the question.
Tyler Robertson:
If people would like to reach out to you, a website, an email, LinkedIn, where would they find you?
Jon White:
Find me? Jon White, Inc.. jonwhiteinc.com, j-o-nwhiteinc.com.
Tyler Robertson:
Awesome. Well, Jon, thank you very much for coming on the show. It's been great to learn about this. I think this is a fascinating thing. I can tell you there's going to be a lot more episodes talking about all the new technologies, right? Predictive analytics, robots driving cars, electrification. It is a big world ahead
Jon White:
Yes.
Tyler Robertson:
... of us in our space. So I'm sure we'll get you back on here to talk more again. So, everybody, we're going to call this an episode, and I want to again to appreciate everyone's time. If you're watching us on YouTube, match that subscribe button. If you're listening to us on Apple Podcast or our Podcast Player, hit the like, comment, share. All those things help us tremendously to getting the reach out there. We appreciate you. We have a lot of things going on here, a lot of great episodes. And I'll end this like in every episode, it's not just Diagnostics, it's Diagnostics Done Right. But quickly, diagnostics is going to be predictive, not reactive. The future's coming.
Jon White:
Yeah.
Tyler Robertson:
Thank you for watching and listening.